Almost four years later, the FASTEN project – Flexible and Autonomous Manufacturing Systems for Custom-Designed Products – came to an end. The objective, successfully achieved through two pilots installed in Brazil and Portugal, involved the development and demonstration of an integrated and modular structure for efficient production of customised products applied to the industry. Researchers incorporated different technologies into the structure: flexible robotics, additive production and simulation-optimisation in manufacturing and logistical systems focused on low-cost mass customisation.
There were two use cases for FASTEN: European and Brazilian. The first case involved EMBRAER (units in Brazil and Portugal), a company operating in the aerospace industry. EMBRAER provided conditions for the development of adaptable robotics for pick & place, while providing improved support for the decision and management of the wing assembly line.
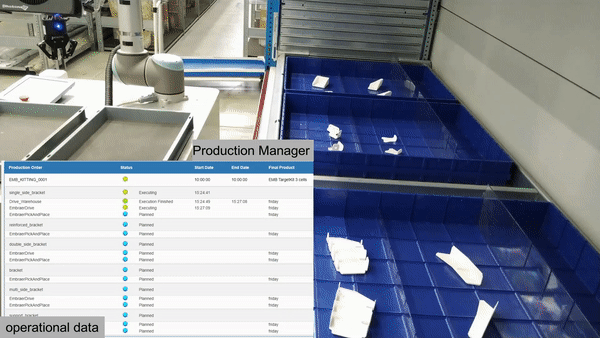
The second case study involved the German multinational Thyssenkrupp, whose activity focuses on the areas of industrial engineering and steel production, with emphasis on the elevator segment. The company’s expertise eased the construction of an Intelligent Robotic Additive Manufacturing and a set of predictive simulation and optimisation tools capable of designing an ideal manufacturing network system, performing real-time monitoring.
“The developments of FASTEN will improve the responsiveness of technical assistance services and the tasks of parts recovery and kit preparation for production lines. In addition, they will also reduce operating and stock costs, increase manufacturing flexibility for the supply of spare parts and for the resizing, modelling and replacement of parts and a faster and more reliable supply of components for production lines”, explained César Toscano, a researcher at INESC TEC’s Centre for Enterprise Systems Engineering (CESE), leading this project at INESC TEC.
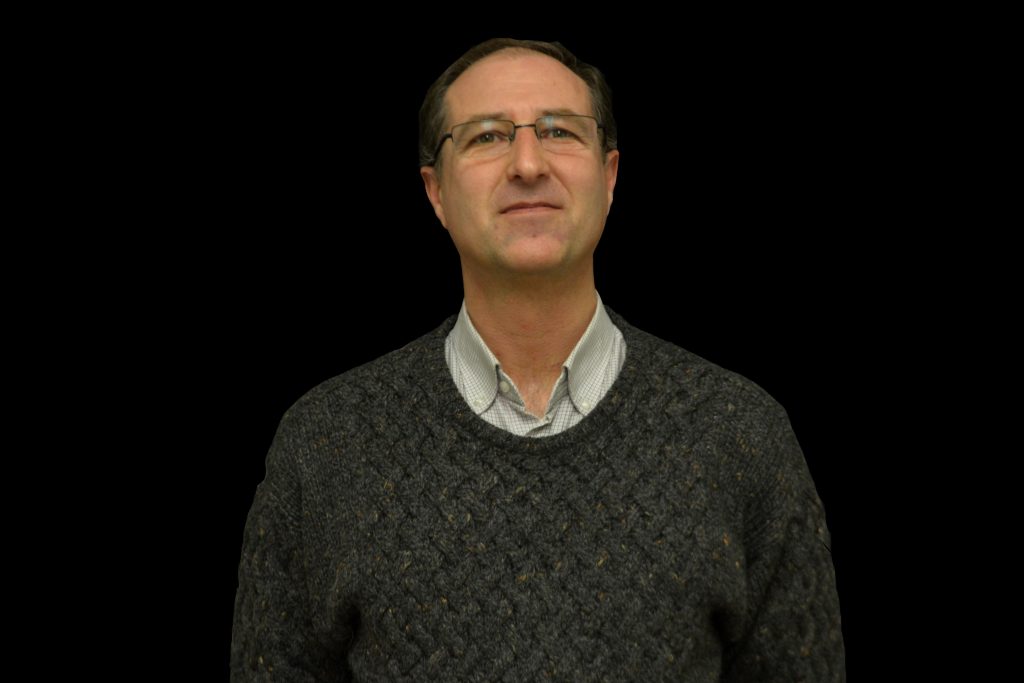
In terms of Technology Readiness Level, the results were fixed at level 7 (Complete System). Therefore, the technology developed is ready to be exploited by the market. The partners that make up the consortium will proceed with exploration and commercialisation plans for the 24 results identified in the FASTEN project.
The project’s final meeting was held online in June, and ended with an overall positive assessment with regard to the results achieved and the Brazil-Europe collaboration. The session was attended by the projects’ coordinators from INESC P&D Brasil and INESC TEC, in addition to the consortium members represented by the partners Politecnico di Milano, Intellimech, PACE/TXT, EMBRAER, Thyssenkrupp, BRADEL, Pontifical Catholic University of Rio Grande do Sul, Federal University of Santa Catarina, Federal University of Bahia and Federal University of Goiás.
Coordinated by researcher César Toscano (CESE), FASTEN’s INESC TEC team included CESE researchers César Toscano, João Pedro Basto, Hugo Miguel Ferreira, Narciso Sobral, Roberto Vita, Jorge Pinho de Sousa, José Soeiro Ferreira and Rui Correia Dias, as well as Rafael Arrais, Carlos Costa, António Paulo Moreira, Germano Veiga, João Souza, Luís Rocha, Pedro Miguel Melo, and Sérgio Teixeira from the Centre for Robotics in Industry and Intelligent Systems (CRIIS)
The researchers mentioned in this news piece are associated with INESC TEC, UP-FEUP and UTAD.